Struggling with Asset Maintenance?
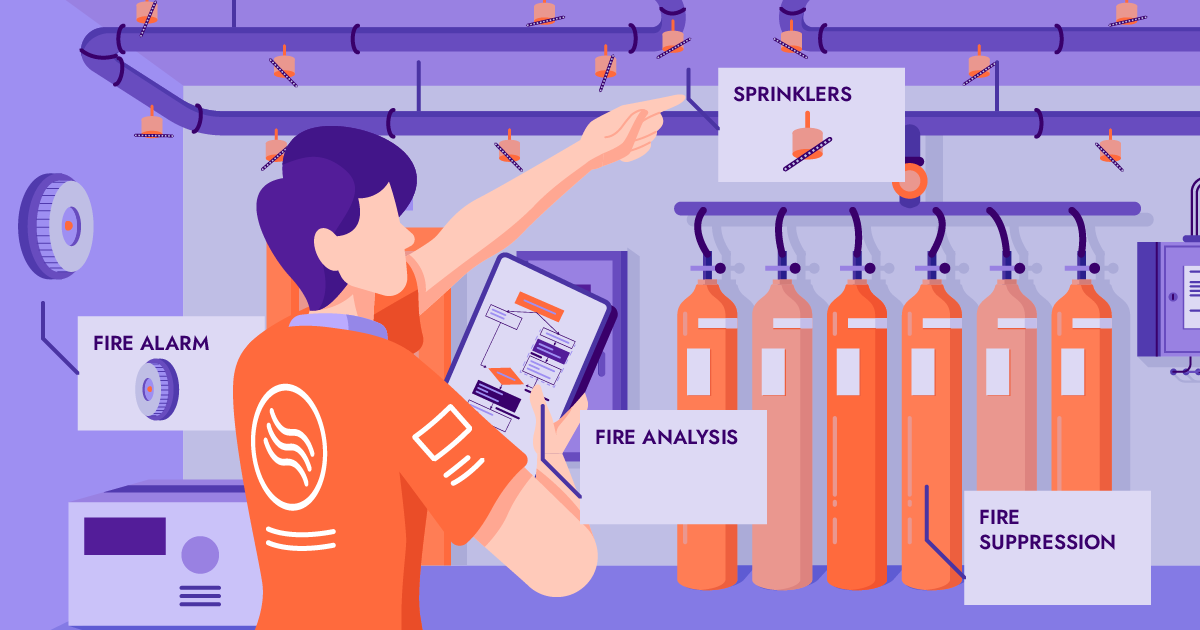
Are You Struggling with Asset Maintenance? Discover the Essential Steps for HVAC Managers
Struggling with HVAC asset upkeep? You’re not alone. Many managers face challenges in keeping systems efficient, from routine checks to urgent repairs. Overcome these hurdles with our guide, featuring top asset management solutions tailored for HVAC operations. Learn how our user-friendly asset management software, FieldInsight, simplifies tasks, minimizes downtime, and cuts costs. Ensure your HVAC systems always perform at their best with proven strategies and tools.
Understanding Asset Management: What It Means for HVAC Managers
Defining Asset Management
Asset management involves the regular upkeep, repair, and management of equipment to ensure optimal performance and longevity. For HVAC (Heating, Ventilation, and Air Conditioning) systems, this is crucial due to their complexity and importance in maintaining indoor air quality and comfort. Effective asset management reduces the risk of unexpected failures and extends equipment lifespan.
For HVAC business operation managers, this includes routine inspections, cleaning, repairs, and the replacement of worn-out components. Regularly inspecting and servicing HVAC systems allows managers to identify potential issues before they escalate into major problems. This proactive approach not only minimizes downtime but also enhances the overall reliability of the systems.
The Role of Asset Management Software in HVAC Operations
To manage these tasks effectively, HVAC businesses and operation managers often rely on asset management tools like FieldInsight. Our software provides a comprehensive solution for tracking and scheduling tasks, ensuring that nothing is overlooked. Asset management software helps organize operations by keeping detailed records of each piece of equipment, including its history, current condition, and future needs.
One of the key benefits of using asset management software is its ability to automate many aspects of operations. For example, the software can generate reminders for upcoming inspections and repairs, ensuring that all tasks are performed on schedule. This automation reduces the administrative burden on HVAC businesses and their managers, allowing them to focus more on strategic planning and less on routine tasks.
The Importance of Regular Operations
Regular operations are essential for the optimal performance of HVAC systems. These operations include various tasks such as:
- Inspections: Regular inspections help identify minor issues before they become major problems. Technicians check for signs of wear and tear, leaks, and other potential issues that could affect the performance of the HVAC system. Early detection through regular inspections prevents minor glitches from escalating into significant, costly disruptions.
- Cleaning: Dust and debris can accumulate in HVAC systems over time, reducing their efficiency and leading to higher energy consumption. Regular cleaning of filters, ducts, and other components helps maintain optimal airflow and system performance. This task is crucial for preventing unnecessary strain on HVAC systems.
- Repairs: Addressing repairs promptly is crucial to prevent minor issues from escalating. Quick repairs can avoid costly downtime and extend the life of HVAC equipment. By implementing a robust asset management solution, businesses can systematically track and analyze the performance of their HVAC units.
- Component Replacements: Some parts of HVAC systems, such as filters and belts, have a limited lifespan and need to be replaced regularly. Keeping track of these replacements ensures that the system operates smoothly and efficiently. This proactive strategy utilizes insights from asset management software to optimize schedules.
Benefits of Effective Asset Management Tool
Effective asset management offers several benefits, including:
- Enhanced System Efficiency: Well-maintained HVAC systems operate more efficiently, consuming less energy and reducing utility costs.
- Increased Equipment Lifespan: Regular upkeep extends the life of HVAC equipment, delaying the need for costly replacements.
- Improved Indoor Air Quality: Clean HVAC systems provide better air quality, contributing to the health and comfort of building occupants.
- Reduced Downtime: Proactive asset management minimizes unexpected breakdowns, ensuring continuous operation.
Understanding and implementing effective asset management is crucial for HVAC businesses. By utilizing asset management software like FieldInsight and adhering to regular operations, managers can ensure the reliability, efficiency, and longevity of their customers’ HVAC systems. This proactive approach not only saves time and money but also enhances service quality and customer satisfaction.
A Systematic Approach to HVAC Asset Management
Introduction to a Systematic Approach to HVAC Operations
Managing HVAC operations effectively requires a systematic approach, which is crucial for any business looking to enhance operational efficiency and system reliability. This comprehensive method encompasses several key strategies: regular diagnostics, predictive maintenance powered by data analytics, and a streamlined workflow for maintenance teams.
Regular Diagnostics: Enhancing HVAC System Health
Consistent check-ups and diagnostics are fundamental to maintaining the health of HVAC systems in any HVAC business. These routine inspections, facilitated by advanced asset management software, play a crucial role in identifying potential issues at their onset. Early detection through regular diagnostics helps prevent minor glitches from escalating into significant, costly disruptions.
Implementing a robust asset management solution allows businesses to systematically track and analyze the performance of their HVAC units. This technological integration supports detailed assessments of system functionalities, such as airflow, thermostat operations, and energy efficiency. By monitoring these parameters, businesses can ensure that their HVAC systems are not only meeting performance standards but are also operating at peak efficiency.
Moreover, regular diagnostics contribute to a proactive strategy. By scheduling frequent evaluations, businesses can create a data-driven approach to asset management. This strategy utilizes insights from asset management software to optimize schedules and reduce unnecessary expenditures on emergency repairs.
Predictive Maintenance Using Data Analytics
Predictive maintenance is a game-changer in HVAC business operations, allowing you to stay one step ahead of potential failures. This method leverages data analytics, a core feature of advanced enterprise asset management software, to accurately forecast when and where a component might fail. By continuously analyzing asset data, such as usage patterns and historical performance metrics, predictive maintenance tools enable you to pinpoint the exact timing for necessary repairs or replacements before issues arise.
Integrating asset tracking capabilities, these analytics consider the entire asset lifecycle management, ensuring each component is monitored from installation to replacement. This proactive approach not only minimizes the risk of unexpected downtime but also optimizes schedules, improving resource allocation and efficiency.
An enterprise asset management system enhances this process by providing a robust platform where all asset data is integrated and analyzed in one place. This comprehensive asset management solution not only tracks real-time conditions but also forecasts long-term trends, helping you make informed decisions that boost overall system reliability and extend the lifespan of your HVAC equipment.
By adopting such a strategic approach, your HVAC business can achieve a significant reduction in operational costs and improve service quality. This results in higher customer satisfaction and a stronger competitive edge in the market.
Streamlined Workflow for Maintenance Teams
Implementing a streamlined workflow is crucial for efficient and effective HVAC operations. An asset management platform centralizes all activities, facilitating quick responses and coordinated actions. This integration allows teams to manage tasks effectively and document every step, boosting productivity.
With user-friendly features, these platforms support remote asset management, enabling teams to track assets throughout their lifecycle from any location. By adopting a unified asset management system, businesses can enhance the reliability and efficiency of their HVAC systems, ensuring optimal performance and supporting sustainable practices.
Why You Should Adopt a Proactive Asset Management Strategy
From Reactive to Proactive Management
Transitioning from reactive to proactive management transforms HVAC operations. This shift not only saves time and money but also enhances system reliability and efficiency. Proactive strategies, supported by robust asset management software, enable HVAC businesses to anticipate issues and address them before they escalate.
Reactive management, which involves fixing problems as they arise, can lead to frequent disruptions and higher costs. In contrast, proactive management focuses on preventing issues before they occur. This approach includes routine inspections, timely repairs, and the use of predictive analytics to foresee potential failures.
Cost and Time Savings
Proactive management reduces the frequency of repairs and replacements, leading to significant cost savings. It also minimizes downtime, ensuring uninterrupted HVAC system operation. By implementing an asset management solution, you can effectively track activities and optimize resource use, further reducing costs.
For example, scheduling regular inspections and cleanings can prevent minor issues from becoming major repairs, saving both time and money. Additionally, predictive maintenance tools can help you plan for necessary parts and labor in advance, avoiding the higher costs associated with emergency repairs.
Enhanced System Reliability and Efficiency
Regular maintenance and predictive analytics improve the reliability and efficiency of HVAC systems. This results in better performance, lower energy consumption, and extended equipment lifespan. An asset tracking system can help monitor the condition and performance of HVAC components, ensuring they operate at peak efficiency.
Efficient HVAC systems consume less energy, which translates to lower utility bills and a reduced environmental impact. By maintaining optimal performance, businesses can also enhance indoor air quality, contributing to the health and comfort of occupants.
Improved Customer Satisfaction
Reliable HVAC systems ensure comfortable indoor environments, leading to higher customer satisfaction. Satisfied customers are more likely to stay loyal and recommend your services to others. By leveraging enterprise asset management tools, you can maintain high service standards and enhance customer experiences.
Happy customers are essential for business growth. When your HVAC systems consistently perform well, it builds trust and reliability, encouraging repeat business and positive word-of-mouth referrals.
Implementing a Proactive Asset Management Strategy
Steps to Implement the Strategy
Implementing a proactive asset management strategy involves several key steps. This approach helps ensure that your HVAC systems are maintained efficiently and effectively, reducing downtime and extending the life of your equipment. Here’s a detailed guide to help you get started:
- Conduct a Thorough Assessment of Current ProcessesBegin by evaluating your existing processes. This assessment should identify strengths and weaknesses in your current approach to managing assets. Look for areas where tasks are frequently delayed, missed, or inadequately performed. Gather data on equipment performance, history, and downtime incidents to get a comprehensive understanding of your current operations.
A detailed assessment will provide insights into inefficiencies and areas for improvement. This can involve interviews with maintenance staff, reviews of records, and analysis of equipment performance data.
- Set Clear ObjectivesOnce you have a clear picture of your current processes, set specific, measurable, achievable, relevant, and time-bound (SMART) objectives for your proactive strategy. These objectives might include reducing equipment downtime, extending the asset lifecycle, and improving overall system efficiency. Having clear goals will help you track progress and measure the success of your strategy.
Clear objectives ensure that your efforts are aligned with business goals. For example, an objective might be to reduce HVAC system downtime by 20% within the next year.
- Develop a Structured PlanA structured plan is crucial for implementing a proactive strategy. This plan should outline the specific tasks required for each piece of equipment, the frequency of these tasks, and the personnel responsible for completing them. Use asset management software to organize and schedule these tasks. The best asset management software will help you track activities, ensure compliance with schedules, and provide reminders for upcoming tasks.
A detailed plan should include checklists, standard operating procedures, and timelines for each task. This ensures consistency and thoroughness in activities.
- Invest in Asset Management Tools and TechnologiesTo effectively manage assets and track activities, invest in advanced asset management tools and technologies. Asset tracking software and enterprise asset management software can provide real-time data on equipment condition, history, and upcoming service needs. These tools help streamline operations and ensure that all tasks are completed on time.
Investing in the right tools can significantly enhance your capabilities. Look for software that offers features like mobile access, real-time monitoring, and integration with other business systems.
- Implement Predictive Maintenance TechniquesPredictive maintenance uses data analytics and monitoring technologies to predict when equipment is likely to fail, allowing you to address issues before they cause downtime. Implementing predictive maintenance involves installing sensors on critical equipment to monitor performance indicators such as temperature, vibration, and pressure. The data collected can be analyzed using asset management software to forecast potential failures and schedule maintenance accordingly.
Predictive maintenance can transform your approach from reactive to proactive. By analyzing trends and patterns, you can anticipate issues and prevent them before they occur.
- Train and Develop Maintenance PersonnelYour maintenance team plays a crucial role in the success of your proactive strategy. Provide regular training to ensure your team is skilled in using the latest asset management tools and technologies. Training should also cover best practices for performing tasks and responding to equipment issues. A well-trained team will be more effective in managing assets and maintaining system reliability.
Continuous training and development keep your team updated on the latest industry standards and technologies. This ensures they can effectively implement the strategy.
- Monitor and Adjust the StrategyContinuously monitor the effectiveness of your proactive strategy. Use asset tracking software to collect data on activities, equipment performance, and downtime incidents. Regularly review this data to identify trends and areas for improvement. Adjust your plan as needed to address any emerging issues and ensure that your strategy remains aligned with your objectives.
Regular reviews and adjustments ensure that your strategy remains effective and responsive to changing conditions. Use data analytics to make informed decisions and continuously improve processes.
- Foster a Culture of Continuous ImprovementEncourage a culture of continuous improvement within your maintenance team and across the entire organization. Regularly solicit feedback from your team on the effectiveness of the strategy and identify opportunities for improvement. By fostering a culture that values proactive maintenance and continuous improvement, you can ensure long-term success in managing your HVAC assets.
Creating a culture of continuous improvement involves recognizing and rewarding innovative ideas and improvements. This encourages team members to contribute actively to the success of the strategy.
By adopting a proactive asset management strategy, you can improve system reliability, reduce operational costs, and enhance customer satisfaction. Regular diagnostics, predictive maintenance using data analytics, and a streamlined workflow are key components of this strategy. Investing in the right tools and technologies, along with ongoing training and development, ensures a smoother, more efficient operation that can adapt to future challenges effortlessly.
What You Should Do Now
- Book a Demo. You’ll be in touch with an automation expert who has worked in this space for over 5 years, and knows the optimal workflow to address your needs.
- If you’d like access to free articles about managing HVAC workflows, go to our blog.
- If you know someone who’d enjoy reading this page, share it with them via email, Linkedin, Twitter, or Facebook.