Roller Conveyor Maintenance Guide: Preventive and Scheduling Best Practices
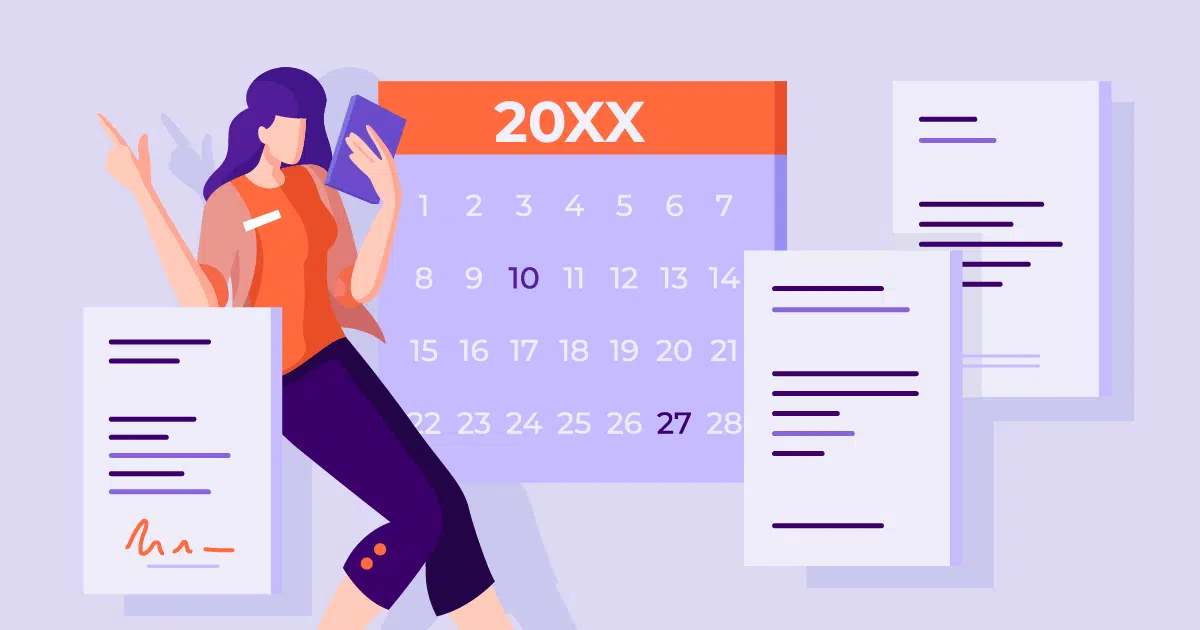
Roller conveyors play a vital role in various industries, allowing for the smooth and efficient movement of goods and materials. However, to ensure their optimal performance and extend their lifespan, regular maintenance is essential.
In this comprehensive roller conveyor maintenance guide, we will delve into the world of preventive and scheduling best practices.
By implementing these strategies, you can minimize downtime, reduce costly repairs, and maximize the efficiency of your roller conveyors.
So, let’s dive in and discover how to keep your roller conveyors in top shape with the help of preventive maintenance software.
The Basics of Roller Conveyors
To understand how to effectively maintain roller conveyors, let’s start with the basics. A typical roller conveyor consists of several key components, including rollers, frames, belts, and supports. These components work together to transport items along the conveyor line. Routine maintenance is necessary to keep each component in optimal condition.
First and foremost, it’s important to inspect the rollers regularly. Check for any signs of wear and tear, such as uneven surfaces, damaged bearings, or misaligned rollers. Replace any worn or damaged rollers promptly to prevent further issues.
Next, examine the frames and supports for any signs of damage or misalignment. Ensure that they are securely fastened and aligned correctly. Any loose or misaligned frames can cause instability and affect the overall performance of the conveyor system.
Lastly, pay attention to the belts or chains that connect the rollers. Look for signs of fraying, stretching, or excessive tension. Tighten or replace any loose or damaged belts to maintain proper functionality.
The Importance of Roller Conveyor Maintenance
Regular field service maintenance is not just a good practice; it is essential for the smooth operation and longevity of roller conveyors. Neglecting maintenance can lead to a range of problems, including increased downtime, decreased productivity, and higher repair costs.
By conducting routine maintenance, you can identify and address potential issues before they escalate. This proactive approach minimizes unexpected breakdowns and ensures that your roller conveyors operate at peak performance. Moreover, well-maintained conveyors contribute to a safe working environment and reduce the risk of accidents.
Daily Inspection and Maintenance Checks for Roller Conveyors
Performing daily inspection and maintenance checks is a fundamental part of roller conveyor maintenance. These checks help identify and address minor issues before they become major problems. Here are some key tasks to include in your daily maintenance routine:
Clean the conveyor: Remove any debris, dust, or residue that may accumulate on the rollers, belts, or frames. This ensures smooth operation and prevents contamination.
Inspect rollers: Check each roller for signs of wear, misalignment, or damage. Replace any worn or damaged rollers promptly to prevent disruptions.
Examine belts or chains: Inspect the belts or chains for signs of wear, tension, or damage. Adjust or replace them as necessary to maintain proper operation.
Lubricate moving parts: Apply lubrication to the rollers, bearings, and other moving parts as recommended by the manufacturer. Lubrication reduces friction and prolongs the lifespan of the components.
Check safety features: Ensure that all safety guards, emergency stops, and sensors are functioning correctly. Address any malfunctions immediately to ensure a safe working environment.
By incorporating these daily maintenance tasks into your asset management, you can prevent potential issues and keep your roller conveyors running smoothly.
Scheduling Routine Maintenance for Roller Conveyors
In addition to daily checks, it’s crucial to establish a comprehensive maintenance schedule for your roller conveyors. A well-planned schedule ensures that maintenance tasks are performed regularly and systematically. Here are some key steps to consider when creating a maintenance schedule:
Determine maintenance intervals: Assess the manufacturer’s recommendations and industry standards to determine the frequency of maintenance tasks. Factors such as conveyor usage, load capacity, and operating conditions may influence the intervals.
Create a checklist: Develop a detailed checklist of maintenance tasks to be performed during each maintenance cycle. Include items such as roller inspection, belt replacement, lubrication, and safety checks.
Assign responsibilities: Clearly define who is responsible for each maintenance task. Assigning specific roles ensures accountability and helps streamline the maintenance process.
Document maintenance activities: Keep a record of all maintenance activities performed, including dates, tasks completed, and any issues encountered. This documentation serves as a valuable reference for future maintenance and troubleshooting.
By adhering to a well-designed maintenance schedule, you can stay proactive in keeping your roller conveyors in optimal condition and minimize the risk of unexpected breakdowns.
The Preventive Approach to Roller Conveyor Maintenance
Preventive maintenance is a proactive strategy that focuses on identifying and addressing potential issues before they cause disruptions. Implementing a preventive maintenance program for your roller conveyors offers several benefits:
Enhanced equipment lifespan: Regular maintenance prevents premature wear and extends the overall lifespan of your roller conveyors.
Reduced downtime: By identifying and addressing potential issues early on, you can minimize unplanned downtime and maintain productivity.
Cost savings: Preventive maintenance helps avoid costly repairs and replacements by addressing minor issues before they escalate.
To implement a preventive maintenance strategy, consider the following steps:
Conduct regular inspections: Perform comprehensive inspections at scheduled intervals to identify any signs of wear, misalignment, or damage.
Replace worn components: Promptly replace any worn or damaged rollers, belts, or chains to prevent further issues.
Lubricate as needed: Apply lubrication to the moving parts as recommended by the manufacturer to reduce friction and ensure smooth operation.
Monitor performance: Regularly monitor the performance of your roller conveyors, including factors such as speed, noise levels, and overall efficiency. Any deviations from normal operation should be investigated promptly.
By adopting a preventive approach to roller conveyor maintenance, you can maximize the lifespan and performance of your equipment while minimizing disruptions.
Cleaning and Lubrication: Key Tasks in Roller Conveyor Maintenance
Cleaning and lubrication are critical aspects of roller conveyor maintenance. Proper cleaning ensures the removal of debris, dust, and contaminants that can hinder performance, while lubrication reduces friction and prevents premature wear. Here are some key tasks to consider:
Cleaning the rollers and belts: Regularly clean the rollers and belts using a mild detergent or cleaning solution. Remove any accumulated debris, dust, or residue to maintain smooth operation.
Inspecting and cleaning bearings: Check the bearings for signs of dirt, debris, or lack of lubrication. Clean and lubricate them as needed to prevent damage and ensure optimal performance.
Lubricating moving parts: Apply lubrication to the rollers, bearings, and other moving parts as recommended by the manufacturer. Use the appropriate lubricant and follow the recommended intervals to ensure proper lubrication.
Remember, excessive lubrication can attract more debris, so it’s essential to strike the right balance. Follow the manufacturer’s guidelines and consult with maintenance experts if needed.
Dealing with Common Roller Conveyor Issues
Despite regular maintenance efforts, roller conveyor mechanism parts may encounter common issues. Knowing how to identify and address these problems promptly can help minimize downtime and prevent further damage. Here are a few common issues and troubleshooting tips for your roller maintenance:
Roller misalignment: Misaligned rollers can cause items to veer off course or create uneven movement. Use a level or laser alignment tool to realign the rollers as needed.
Belt tracking problems: If the conveyor belt starts to veer to one side, it can cause jams and disruptions. Adjust the tracking mechanism or consult the manufacturer’s guidelines for corrective actions.
Excessive noise or vibration: Unusual noise or excessive vibration may indicate loose or worn components. Inspect and tighten any loose parts or replace worn components as necessary.
Conveyor jams: Items getting stuck or jammed on the conveyor can disrupt the workflow. Identify the cause of the jam and address it promptly, ensuring the safe removal of any obstructions.
If you encounter persistent or complex issues, it’s advisable to consult with a professional technician or contact the manufacturer for assistance.
Record Keeping: A Vital Part of Roller Conveyor Maintenance
Maintaining accurate and detailed records of maintenance activities is crucial for effective roller conveyor maintenance. A comprehensive maintenance log provides valuable information and insights for future maintenance, troubleshooting, and decision-making. Here are the key aspects of record keeping:
Maintenance schedule and tasks: Document the scheduled maintenance tasks and intervals in your maintenance log. This ensures that tasks are performed on time and allows for easy tracking and planning.
Task completion and observations: Record details of each maintenance task performed, including dates, tasks completed, and any observations made during the process. This information helps identify patterns, track performance, and troubleshoot recurring issues.
Repairs and replacements: Document any repairs or component replacements carried out, along with the reasons and dates. This log serves as a reference for future maintenance and helps identify any recurring issues or problematic components.
Equipment performance: Record any notable observations regarding the performance of your roller conveyors, such as changes in speed, noise levels, or efficiency. This data can help detect emerging issues and guide maintenance decisions.
By maintaining detailed records, you can establish a comprehensive maintenance history, make informed decisions, and enhance the overall efficiency of your roller conveyor maintenance efforts.
Safety Measures in Roller Conveyor Maintenance
Safety should be a top priority during roller conveyor maintenance. Working with heavy machinery and moving parts can pose risks if proper precautions are not taken. Here are some essential safety measures to follow:
Lockout/Tagout (LOTO): Implement a lockout/tagout procedure to isolate the conveyor system from its power source before conducting any maintenance tasks. This ensures that the equipment cannot be started accidentally during maintenance.
Personal protective equipment (PPE): Wear appropriate PPE, such as safety glasses, gloves, and protective clothing, to protect against potential hazards.
Training and awareness: Ensure that maintenance personnel are properly trained in operating and maintaining roller conveyors. Regularly update their knowledge and provide safety refresher training.
Clear communication: Establish clear communication protocols between maintenance personnel and operators to ensure everyone is aware of maintenance activities and potential hazards.
Regular inspections: Regularly inspect the safety features of the roller conveyor system, such as emergency stops, safety guards, and sensors. Repair or replace any faulty safety equipment immediately.
Always prioritize safety and encourage a safety-conscious culture in your maintenance practices to protect both personnel and equipment.
Utilizing FieldInsight for Roller Conveyor Maintenance
To streamline and optimize your roller conveyor maintenance processes, consider leveraging maintenance management software like FieldInsight. FieldInsight offers a comprehensive solution for organizing and tracking maintenance tasks, managing schedules, and generating reports. Here are some key benefits of using FieldInsight:
Streamlined task management: Assign and track maintenance tasks, set reminders, and receive notifications for upcoming tasks, ensuring nothing falls through the cracks.
Maintenance history and documentation: Store and access detailed maintenance records, including task completion dates, observations, and repairs. This enables easy tracking, analysis, and decision-making.
Preventive maintenance scheduling: Set up preventive maintenance schedules within FieldInsight, ensuring that routine maintenance tasks are performed on time and consistently. Avoid debris buildup, excessive wear, structural damage, material spillage, belt slippage, and more with regular planned preventative maintenance.
Real-time updates and collaboration: Facilitate seamless communication and collaboration among maintenance teams, allowing for real-time updates and efficient coordination.
Data-driven insights: FieldInsight provides analytical reports and performance metrics that can help identify trends, optimize maintenance strategies, and improve overall equipment reliability. Ensure you have all the right tools for conveyor belts, roller bearings, and more. With a field service software you can save time in your conveyor maintenance plan to ensure normal conveyor operation is consistent.
Conveyor Belt Maintenance Takeaways
Regular and proactive maintenance is the key to ensuring the smooth operation and extended lifespan of your roller conveyors. By implementing preventive and scheduled maintenance practices, performing daily inspections, and incorporating cleaning and lubrication tasks, you can prevent major issues, reduce downtime, and enhance overall efficiency.
Remember, proper record keeping, prioritizing safety measures, and utilizing maintenance management software like FieldInsight can significantly streamline your maintenance processes and help you achieve optimal results.
So, don’t wait! Start implementing these best practices today and explore the benefits of FieldInsight as a comprehensive solution for your roller conveyor maintenance needs. Your roller conveyors will thank you with extended service life and reliable performance.
What You Should Do Now
- Book a Demo. You’ll be in touch with an automation expert who has worked in this space for over 5 years, and knows the optimal workflow to address your needs.
- If you’d like access to free articles about managing HVAC workflows, go to our blog.
- If you know someone who’d enjoy reading this page, share it with them via email, Linkedin, Twitter, or Facebook.