Preventive Maintenance Optimization Guide For Service Managers
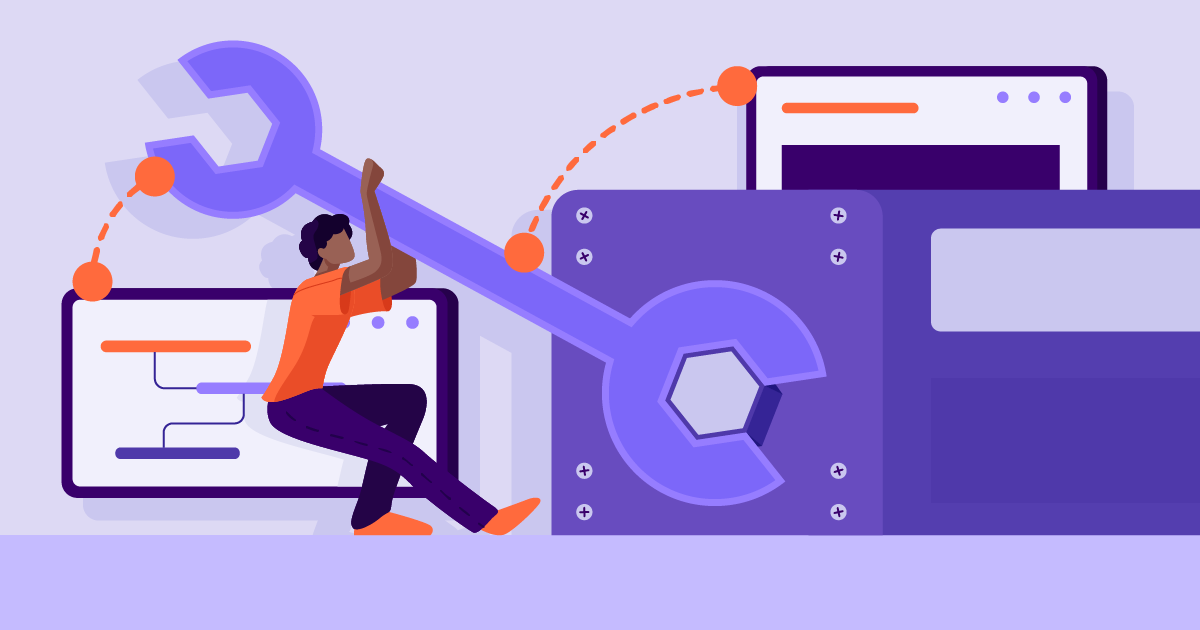
Preventive maintenance is vital to maintain assets and ensure longevity and high quality performance, but it can be hard to keep track of when you have a busy business. To sync your maintenance technicians, maintenance tasks, and documentation, you need to have the right systems in place in your business.
In this guide we will dive into how to optimize your PM program and get the most out of your maintenance work.
Getting Started with Preventive Maintenance
Preventive maintenance is the planned process of improving equipment running and reducing the chance of equipment failing from occurring. The decision process behind the right frequency of PM maintenance tasks will rely on the manufacturer’s recommendations, your client contracts and availability of your maintenance technicians. Preventive maintenance software can be used to enhance your workflow and keep track of your systems.
Measuring the Effectiveness of Preventive Maintenance
Is your PM program effective? To determine this, you need to take a look at your asset maintenance tasks and how well they eliminate functional failure in proportion to the costs of your maintenance tasks.
Creating a plan for your maintenance team to review your work can be beneficial to discover how you can improve your workflow and in reducing costs of maintenance tasks.
Top 5 Reasons You Should Conduct Ongoing Preventive Maintenance Optimization
Preventive maintenance tasks have many benefits for both your business and your customers. With the right preventive maintenance program and optimization systems in place you could:
- Discover ways to free up your time
- Boost consistency in your workflow
- Find ways to reduce costs
- Better train and inform your maintenance team
- Create simpler solutions and continuous improvement
Top Preventive Maintenance Problems and Challenges
While preventive maintenance is hugely beneficial, there are also some problems and challenges that can hold up your maintenance team. Asset management involves a lot of moving parts and endless paperwork at times. Here are the most common problems you may face in the field:
1. Preventive maintenance compliance tracking
Tracking compliance for your assets can be hard when in the field. To help improve your asset reliability, you need to have accurate failure reporting and compliance measured procedures in place.
If your team is using paper based systems to track their work, you will be faced with stale information and possible delays between your office and field. Ensuring that your assets are compliant is crucial in the field service industry, but is often easier said than done.
2. No accountability over preventive maintenance tasks
Your maintenance team has done the work… but where is the proof? Which tech signed off the asset test? Did a copy of the report get sent to your client?
Accountability is a vital part of your PM program and will help you determine what your team has or hasn’t done. Documentation is important in preventing failures for assets and ensuring that your customers can see evidence of the work you have completed. Without a reliable system of software in place, you may find it hard to track your team’s accountability when out in the field.
3. Scheduled maintenance consistency
Preventative maintenance needs to be scheduled at regular intervals in order to become successful at avoiding total failure of an asset. However, without a good schedule in place, it can be hard to ensure that your corrective action is making the effect it needs.
To get the full benefits of routine maintenance activities, you need to sync your scheduled maintenance tasks with your team, and your customers to ensure that your planned jobs can run smoothly. What’s the key to this? Optimization in your PM program.
Preventive Maintenance Optimization Steps
The PM optimization process focuses on eliminating equipment failures and boosting the accountability in your business. Here are the steps you need:
1. Identify critical equipment functions
To begin, you need to know the necessary functions of your assets, and what might be checked in equipment inspections. To discover this, consider what defect could occur that would affect the operation of the asset. Are there specific failure modes? Start to consider these steps for your asset scheduled maintenance tasks.
2. Find common defects and failure modes
Now that you know what could go wrong, how will this impact your asset’s operation? Run an effects analysis to determine the common defects and how your assets will fail to meet their requirements.
3. Identify the severity of asset failure modes
How severe will these defects be? Will there be a large production loss? Can this be fixed with a simple repair, or will this asset be out of order for weeks?
This part of your maintenance reporting optimization is about identifying what will happen if an asset fails and the impact of this on the production line.
4. How to use predictive maintenance tasks
You’ve identified how severe the effects of the asset failure will be, now what tasks can you include in predictive maintenance to avoid this from occurring. For your equipment servicing you can now create steps for your maintenance team to follow to ensure that these root cause analysis problems are avoided.
5. How to include corrective work in your workflow
Find time to schedule maintenance tasks with your failure reporting in mind and train up your team to follow the right steps. A great way to use your preventive maintenance program to best use, is by scheduling your work during your slow season to ensure all the required assets get the attention they need.
An example of these 5 steps would be for a hot water system:
- A critical equipment functions- Thermostat and Pressure relief valve
- Common defect- Build up of debris, or broken thermostat
- Severity of failure modes- No hot water, and can cause internal damage of build up
- PM tasks to use- Regular cleaning, inspection of thermostat and release pressure of valve
- Include in your PM program- Steps to check for leaks, inspect thermostat, release pressure from temperature pressure release valve once a year.
Using Software To Support Your Ongoing Maintenance
Using software in your PM process can boost the reliability centered maintenance in your workflow and help your team better manage your assets.
1. Preventive maintenance + simple repeat scheduling
One of the most common and effective tools a preventive maintenance software includes, is the scheduling features. With the ability to add repeat scheduled maintenance work with just a click, you can save hours of time and eliminate double data entry from your workflow.
You can simply send a notification to your customer to remind them closer to the date and reminders to ensure that your technician has everything they need.
2. Job management + job status tracking
With job management features in a PM optimization software, you can view the status of your jobs to see with a glance what has or hasn’t been completed. This tool allows you to have more insight into how long each job takes and you can easily let your customers know how soon a tech will be at their site.
3. Project management + visibility over budgeting
With more visibility over your budgeting, you can better balance maintenance work vs repair costs to determine the best course of action for an asset. Project management allows you to keep track of all your jobs and projects to ensure that preventive maintenance processes are running smoothly.
4. Computerized maintenance management system + real time data
CMMS and real time data ensure that everyone can stay on the same page. There are many tasks that are involved in field maintenance, and without the help of real time data, you may be dealing with stale information, or the wrong information entirely. Keep your team on track with real time data and the help of automation to do the heavy lifting for your business.
Industries That Conduct Preventive Maintenance Optimization
Do you have a current preventive maintenance program in your business? Many organizations have procedures in place to perform maintenance tasks, without realizing they could be better managing their time with optimization.
Some of the most common field service industries that rely on preventive maintenance optimization are:
1. HVAC
In the HVAC industry, preventive maintenance and a corrective action system is vital to ensure longevity of assets. From air conditioners to refrigeration systems, you need to include planned maintenance to keep assets from developing defects. Preventive maintenance processes can be vital to ensuring that assets are always running smoothly.
2. Fire Protection
Fire Protection is essential to keeping everyone safe in the workplace. Great fire protection software should include; easy scheduling, customer portal access, checklists for maintenance, customer reporting, and flexible customisation options.
3. Plumbing and Electricians
Plumbing and electrical industries both need to have high visibility over their field work and maintenance technicians. That’s why they need software that can provide; automated tools, mobile access, simple documentation, and easy timesheet management.
3. Construction, Civil and Heavy Equipment
Construction, civil, and heavy equipment industries all rely heavily on asset management and it can become frustrating when you have a lack of clarity over your PM process. From payroll, supply chain management, project costing, and of course preventive maintenance tasks, it can all be easily accessed in an automated software to make sure your business is on the same page.
Optimize your business today with a field service software that is flexible to your needs. Get your preventive maintenance tasks on track without the frustration, so you can go from quote to invoice with just a few clicks. Find out how FieldInsight can help your preventative maintenance program level up today.
What You Should Do Now
- Book a Demo. You’ll be in touch with an automation expert who has worked in this space for over 5 years, and knows the optimal workflow to address your needs.
- If you’d like access to free articles about managing HVAC workflows, go to our blog.
- If you know someone who’d enjoy reading this page, share it with them via email, Linkedin, Twitter, or Facebook.